“RAKtherm Suppliers Karachi Pakistan. Sizes available from 20mm to 110mm. Food grade materials for Building construction and potable water supply. Stock Available in Pakistan.
CONTACT +92-321-2248975
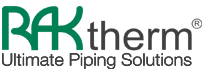
“RAKtherm Suppliers Karachi Pakistan. Sizes available from 20mm to 110mm. Food grade materials for Building construction and potable water supply. Stock Available in Pakistan.
CONTACT +92-321-2248975
Plastic Jali Grating for Drain for liquid water Waste Sewer of Main Gates, Swimming Pool, Industrial Waste, Water Pool, Farm Houses or Cattle Farms etc.
Supplier Dealer and provider in Karachi Lahore Islamabad. Aslo Deliver in Other Cities of Pakistan.
Heavy Duty PVC Grating bears apx 1200lbs weight that any ride Tyre can pass through easily. Please Note that These Plastic Drainage is not manufactured in Pedestrian grade.
Fiber Concept (local made in Pakistan) manufacture These Gratings and Manhole Covers in Pedestrian and Heavy Vehicle Grade.
AGM PVC Pipe Suppliers. AGM PVC Pipe fitting for Hot and Cold water supply drainage sewer and AC drain plumbing installation system. Price list supplier and dealers in Karachi & Islamabad Pakistan. +92-321-2248975
Upvc Pipes and Fittings are available for water drain sewer ASTM quality standard. Size Range from 1/2″ to 8″ for both Pipe and Fitting. made in KSA Saudi Arabia.
CPVC pipe fittings for hot water supply in geyser lines size range available from 1/2″ to 2″. Made in KSA Saudi Arabia. Color Grey for all items like pipe, fitting and brass thread items.
AGM UPVC and CPVC pipes are produced in 6 meter length with plain end .
AGM pipes are produced according to ASTM D-2241 SDR. white colour in length of 6 meters with socket or plain end also other lengths are produced upon request.
complete systems of Pipes covered with production of all fittings. Objective of AGM complete system is covered for production of fittings also a part from Pipes.
ADVANTAGES OF AGM
HIGH FLEXILIBILITY
EASY TO OINSTALL
SMOOTH AND LOW FRICTION
EASY CONNECTION
HIGH CORROSION RESISTANCE
HIGH MECHANICAL STRENGTH
NON TOXIC
HIGH ELECTRICAL INSULATION
HIGH THERMAL INSULATION
HIGH IMPACT STRENGTH
LONG LIFE
AGM CPVC PIPES & Fittings:
AGM pipes cpvc for hot water supplies are manufactured in inch dimensions for 1/2″ to 2″
AGM pipes spvc schedule 80 are manufactured according to ASTM F-441 specifications
AGM pipes cpvc are normally available in standard length of 6 methers other length can be manufactured available in plain end pipes and made light gray color
Chlorinated poly vinyle chloride (CPVC)
This is a thermoplastic piping material which can be used for higher temperature applications it is a special polymer with a higher glass transition point which means advantages over regular pvc pipes and fittings
cpvc retains its mechanical strength at higher temperature
cpvc 93 degree celsius at max (uPVC at max 59 degree celsius)
cpvc pipes manufacturing standard F-441(Sch-80) & cpvc fittings manufacturing standard F-439 (Sch-80)
AGM CPVC Solvent cement (914)
for Hot & Cold pipes jointing
Sizes available 120ml, 237ml, 475ml & 946ml packing.
Manufacturing standards meet ASTM F-493.
Extremely flammable
Ingredients:
Tetrahydrofuran 109-99-9,
Methyle Ethyle Ketone 78-93-3
cyclehaxanone 108-94-1
Resin 68648-82-8
HMIS rating H-3 F-3 R-1
AGM Cleaner (970)
AGM universal clear cleaner for cleaning pvc, cpvc and abs pipes and fittings, all schedule and diameters
for Hot & Cold pipes jointing
Sizes available 120ml, 237ml, 475ml & 946ml packing.
Manufacturing standards meet as per USA product.
Extremely flammable
Ingredients:
Acetone 67-64-1
Methyle Ethyle Ketone 78-93-3
cyclehaxanone 108-94-1
Resin 68648-82-8
HMIS rating H-3 F-3 R-1
High-density polyethylene (HDPE) or polyethylene high-density (PEHD) is a polyethylene thermoplastic made from petroleum. It takes 1.75 kilograms of petroleum (in terms of energy and raw materials) to make one kilogram of HDPE. HDPE is commonly recycled, and has the number “2” as its recycling symbol. In 2007, the global HDPE market reached a volume of more than 30 million tons[1].
Contents
1 Properties
2 Applications
3 See also
Properties
HDPE has little branching, giving it stronger intermolecular forces and tensile strength than lower-density polyethylene. The difference in strength exceeds the difference in density, giving HDPE a higher specific strength.[2] It is also harder and more opaque and can withstand somewhat higher temperatures (120 °C/ 248 °F for short periods, 110 °C /230 °F continuously). High-density polyethylene, unlike polypropylene, cannot withstand normally-required autoclaving conditions. The lack of branching is ensured by an appropriate choice of catalyst (e.g., Ziegler-Natta catalysts) and reaction conditions. HDPE contains the chemical elements carbon and hydrogen.
Applications
HDPE is resistant to many different solvents and has a wide variety of applications, including:
Telecom Ducts
Containers
Laundry detergent bottles
Milk jugs
Fuel tanks for vehicles
Plastic lumber
Folding tables
Folding chairs
Storage sheds
Portable basketball system bases
Plastic bags
Geomembrane for hydraulic applications (canals, bank reinforcements…) and the containment of certain chemicals
Chemical-resistant piping systems
Heat-resistant fireworks display mortars
Geothermal heat transfer piping systems
Natural gas distribution pipe systems
Water pipes, for domestic water supply
Coax cable inner insulators (dielectric insulating spacer)
Root barrier
Corrosion protection for steel pipelines
Tyvek
Snowboard rails and boxes
Bottles, suitable for use as refillable bottles
Modern hula hoops
Ballistic plates
Bottle Caps
Breast implants
HDPE is also used for cell liners in subtitle D sanitary landfills, wherein large sheets of HDPE are either extrusion or wedge welded to form a homogeneous chemical-resistant barrier, with the intention of preventing the pollution of soil and groundwater by the liquid constituents of solid waste.
One of the largest uses for HDPE is wood plastic composites and composite wood, with recycled polymers leading the way.
HDPE is also widely used in the pyrotechnics trade. HDPE mortars are preferred to steel or PVC tubes because they are more durable and more importantly they are much safer compared to steel or PVC. If a shell or salute were to malfunction (flowerpot) in the mortar, HDPE tends to rip and tear instead of shattering into sharp pieces which can kill or maim onlookers. PVC and steel are particularly prone to this and their use is avoided where possible.
Milk bottles and other hollow goods manufactured through blow molding are the most important application area for HDPE – More than 8 million tons, or nearly one third of worldwide production, was applied here. Above all, China, where beverage bottles made from HDPE were first imported in 2005, is a growing market for rigid HDPE packaging, as a result of its improving standard of living. In India and other highly populated, emerging nations, infrastructure expansion includes the deployment of pipes and cable insulation made from HDPE. The material has benefited from discussions about possible health and environmental problems caused by PVC and Polycarbonate associated Bisphenol A, as well as, its advantages over glass, metal and cardboard.
See also
Linear low-density polyethylene
Low-density polyethylene
Phillips Disaster
Resin identification code
Ultra-high-molecular-weight polyethylene
Plastic recycling
Medium density polyethylene
More Details:Â http://en.wikipedia.org/wiki/HDPE
Polyvinyl chloride, (IUPAC Poly(chloroethanediyl)) commonly abbreviated PVC, is a thermoplastic polymer. It is a vinyl polymer constructed of repeating vinyl groups (ethenyls) having one of their hydrogens replaced with a chloride group.
Polyvinyl chloride is the third most widely produced plastic, after polyethylene and polypropylene.[3] PVC is widely used in construction because it is cheap, durable, and easy to assemble. PVC production is expected to exceed 40 million tons by 2016.[4]
It can be made softer and more flexible by the addition of plasticizers, the most widely used being phthalates. In this form, it is used in clothing and upholstery, and to make flexible hoses and tubing, flooring, to roofing membranes, and electrical cable insulation. It is also commonly used in figurines and in inflatable products such as waterbeds, pool toys, and inflatable structures. Â
Polyvinyl chloride | |
---|---|
Density | 1390Â kg/m3[1] |
Young’s modulus (E) | 2900-3300 MPa |
Tensile strength(σt) | 50-80 MPa |
Elongation at break | 20-40% |
Notch test | 2-5Â kJ/m2 |
Glass temperature | 82 °C[1] |
Melting point | 100–260 °C[1] |
Vicat B | 85 °C[2] |
Heat transfer coefficient (λ) | 0.16 W/(m·K) |
Effective heat of combustion | 17.95 MJ/kg |
Linear expansion coefficient (α) | 8 10−5/K |
Specific heat (c) | 0.9 kJ/(kg·K) |
Water absorption (ASTM) | 0.04-0.4 |
Price | 0.5-1.25 €/kg |
Polypropylene | |
---|---|
![]() |
|
Identifiers | |
CAS number | 9003-07-0Â ![]() |
Properties | |
Molecular formula | (C3H6)n |
Density | 0.855 g/cm3, amorphous
0.946 g/cm3, crystalline
|
Melting point |
~160 °C
|
 ![]() Except where noted otherwise, data are given for materials in their standard state (at 25 °C, 100 kPa) |
|
Infobox references |
Contents [hide] |
![]() |
This article may need to be wikified to meet Wikipedia’s quality standards. Please help by adding relevant internal links, or by improving the article’s layout. (April 2009) |
Contents [hide] |
![]() |
This section requires expansion. |
Tempertaure | Service life (years) | Permissible working Pressure, for nominal pressure classes (bars) |
||
---|---|---|---|---|
PN 10 | PN 20 | PN 25 | ||
20 C° | 1 | 15.1 | 30.7 | 37.7 |
5 | 14.0 | 28.0 | 35.0 | |
10 | 13.5 | 27.1 | 33.8 | |
25 | 13.2 | 26.4 | 33.0 | |
50 | 12.9 | 25.9 | 32.3 | |
30C° | 1 | 12.8 | 25.6 | 32.0 |
5 | 12.0 | 24.0 | 30.0 | |
10 | 11.7 | 23.5 | 29.3 | |
25 | 11.3 | 22.7 | 28.3 | |
50 | 11.1 | 22.1 | 27.7 | |
40C° | 1 | 11.1 | 22.1 | 27.7 |
5 | 10.4 | 20.1 | 26.0 | |
10 | 10.1 | 20.3 | 25.3 | |
25 | 9.7 | 19.5 | 24.5 | |
50 | 9.2 | 18.4 | 23.0 | |
50C° | 1 | 9.5 | 18.9 | 23.7 |
5 | 8.9 | 17.9 | 22.3 | |
10 | 8.7 | 17.3 | 21.7 | |
25 | 8.0 | 16.0 | 20.0 | |
50 | 7.3 | 14.7 | 18.3 | |
60C° | 1 | 8.3 | 16.5 | 20.7 |
5 | 7.6 | 15.2 | 19.0 | |
10 | 7.2 | 14.4 | 18.0 | |
25 | 6.1 | 12.3 | 15.3 | |
50 | 5.5 | 10.9 | 13.7 | |
70C° | 1 | 6.7 | 13.3 | 16.7 |
5 | 6.0 | 12.0 | 15.7 | |
10 | 5.3 | 10.7 | 13.3 | |
25 | 4.5 | 9.1 | 11.3 | |
50 | 4.4 | 8.8 | 11.0 | |
80C° | 1 | 4.3 | 8.5 | 10.7 |
5 | 8.7 | 12.3 | 13.7 | |
10 | 4.3 | 10.7 | 10.8 | |
25 | 3.9 | 9.3 | 9.8 | |
50 | 3.7 | 7.5 | 9.2 | |
90C° | 1 | 3.8 | 7.5 | 8.4 |
5 | 2.9 | 5.7 | 6.3 |
PPRC Piping System is an absolute solution for distribution application of hot & cold water in all modern residential appartments, commercial buildings, housing societies and various industries due to its high resistance to high temperature and pressure.
PPRC Pipe System is manufactured from Polypropylene Random Copolymer 100% food grade material imported from Euorpe, China, Malaysia or Germany Borealis & Basell. However in Pakistan “Engro” Company is also a supplier of PPRC Resin. Local manufacturers usually purchases from Engro Polymer Company.
Outer Diameter | Welding Depth | Welding Time(sec) | Connection Time (sec) | Cooling Time (sec) |
20 | 14 | 5 | 4 | 2 |
25 | 15 | 7 | 4 | 2 |
32 | 16.5 | 8 | 6 | 4 |
40 | 18 | 12 | 6 | 4 |
50 | 20 | 18 | 6 | 4 |
73 | 24 | 24 | 8 | 6 |
75 | 26 | 30 | 8 | 8 |
90 | 29 | 40 | 8 | 8 |
110 | 32.5 | 50 | 10 | 8 |